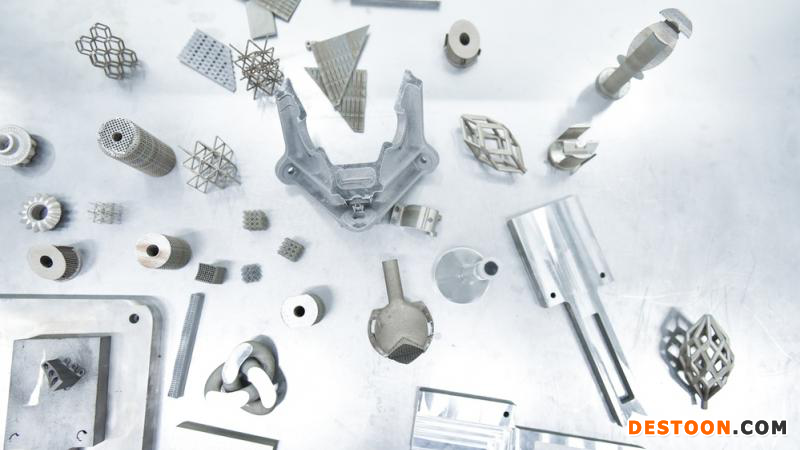
In the nearest future, the obtained composites will be used to grow the spacecraft parts for Russian aircraft industry. The research is conducted under a grant from the Russian Science Foundation; the results are published in Materials.
Scientists from the National University of Science and Technology MISIS, led by Professor Alexandr Gromov developed a method of 3D-printing of alumomatrix (aluminum-based) composite materials with ceramic fillers (aluminum oxide and nitride). The research was conducted in the framework of the project of the Russian Science Foundation. The use of additive technologies allowed increasing the strength of the resulting powder materials by 20%.
Alexander Gromov comments:“For 3D-printing of aluminum details, so-called silumins (alloys of aluminum with silicon, in particular, the compound Al-Si-10Mg) are mainly used as raw materials. However, the demands of the aerospace industry are growing, and scientists are now actively searching for new compositions of alumomatrix composites (including doped ones) to obtain details with improved performance (strength, hardness, resistance to cracking) and low cost, compared to alloys that contain rare earth elements”.
The annual growth rate of the global market of additive technologies exceeds 100%. This can be explained by the advantages of additive technologies for metals compared to traditional industrial technologies: casting, powder metallurgy etc. This includes the ability to create complex 3D-details, reduce the weight of the detail by optimizing the design, increase the strength of the details, as well as the technology for fast and situational production of small-scale details of complex shape. One of the most popular directions is the development of methods of 3D-aluminum printing for aerospace.
In this case, the main task of material scientists is to reduce the detail weight while maintaining the strength characteristics. Nowadays, the metal primarily used in aircraft is titanium. It is a durable, corrosion- and load-resistant material, the only significant disadvantage of which is the high density, 5.4 g/mm. Lightweight and ductile aluminum at the same time has a density of 2.7 g/mm, that is, it is twice as light. However, it is far less strong than titanium. Scientists are actively looking for ways to strengthen aluminum.
Professor Gromov adds:“We managed to increase the strength of aluminum powders due to hardening ceramic additives directly in the process of 3D-printing. Previously, it was believed that obtaining such composites on printers such as SLM is impossible. However, the group was able to create experimental samples of the new powder material on a conventional printer SLM-280 HL, i.e. using selective laser melting”
The proposed methods allow increasing the flexibility of design, reducing the production time of functional prototypes, reducing the weight of the resulting details by 10-20 %.
As noted by Andrey Arnautov, Deputy Director for new projects, UC Rusal:“NUST MISIS scientists have come close to the realization of the long-standing dream of aluminum producers: the full replacement of titanium with aluminum composites. Many researchers have worked on the problem of producing lightweight and durable aluminum composites by traditional metallurgical methods, but the team led by Professor Alexander Gromov has moved even further and is working on growing a 3D-detail from innovative powders”.
Currently, the research team is completing a series of laboratory tests of the resulting batch of material. In the near future, the researchers will switch to the next step of the project, i.e. obtaining the first samples of details from this aluminum-ceramic powder.