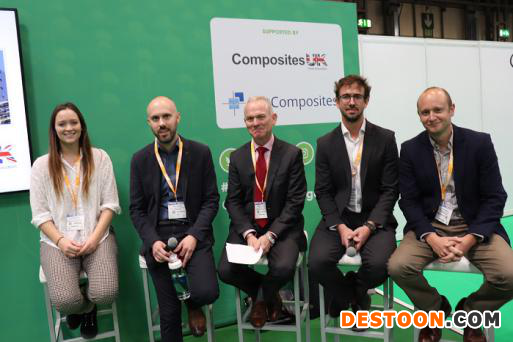
Composites in the Circular Economy was the subject of a lively debate at the Advanced Engineering Conference held at the NEC in Birmingham, UK on 31 October.
Chaired by Stella Job of Composites UK, it involved Lucy Eggleston of the National Composites Centre, Paul Spencer of Gurit, Martin Wright of Polynt Composites, Ben Andrew of ELG Carbon Fibre and Joe Summers of Airborne.
Digitisation
Airborne, with operations in the Netherlands and the UK, specialises in the industrialisation of engineering and manufacturing of durable fibre reinforced composites via automation and digitisation, with a focus on achieving high production rates at radically low conversion costs.
“Composites are inherently sustainable, making planes lighter, wind blades longer and increasing the durability of structures,” Joe Summers observed. “Industry 4.0 will make it cheaper to make composites and reduce waste in the process, but what would be a real breakthrough would be knowing exactly what’s in final composite products to enable and understand all of the processes involved in the creation of a part. This will aid the recycling options for components which we will be able to feed back into the product design.
“Industry 4.0 and near net shape manufacturing are real solutions because if we can make things faster we can reach more markets and achieve the critical mass required.”
At present, he added, the need for light weighting is having more influence in selection than the actual properties of the material.
“What will drive recycling is legislation,” he said. “REACH, for example, obliges companies to register their different chemicals and it wouldn’t take much to extend that requirement upstream.”
Clear route
The recycling rates for stainless steel are now above 90% and those for aluminium over 70%, yet at the moment less than 1% of composites are recycled and this will surely have to change, observed ELG’s Ben Andrew.
ELG is striving to reidentify its recycled carbon fibres as new grades in order to assist future standardisation. © Inside Composites
ELG is striving to reidentify its recycled carbon fibres as new grades in order to assist future standardisation. © Inside Composites
“Our suppliers have a large amount of waste and we have developed a clear route to recycling it, but I believe standardisation is the key to increased recycling industry-wide,” he said. “Composites are inherently flexible in terms of fibre and resin types and that’s a problem when it comes to recycling, so to approach a totally circular economy we need to standardise as much as possible. The plastics industry has gone a long way in this respect, but composites have yet to make significant progress. This challenge will be met by engineers and chemists prioritising design – not just for manufacturing, but also for disassembly and recycling. It’s also a question of reaching the critical mass to allow engineers to push forward on this.”
With the waste material received from its aerospace customers, ELG is striving to reidentify the fibres as new grades, as a positive step in this direction.
GRP
For Martin Wright of Polynt, a manufacturer of speciality polymer resins and intermediates primarily serving the glass reinforced plastic (GRP) market and based in Immingham, UK, the sustainability message has been hijacked by the aluminium and steel industries who have moved its focus onto recycling away from the clear advantages in processing and final products that composites provide.
He acknowledged, however, that GRP is a low value product and a route to its successful recycling has to be found if the industry is not to fall foul of regulation.
“The GRP industry developed at a time when raw materials were very cheap, the price of disposal was zero and labour was the highest cost,” he said. “Now that has changed.”
When it comes to recycling, however, he said that there are a lot of flame retardant treatments containing halogenated chemistry in many GRP composites that are extremely hard to trace.
Stella Job added that GRP is successfully recycled in Germany by being co-processed with other wastes as solid recovered fuel (SRF) in cement kilns. This recovers energy from the organic part, and mineral fillers and glass become feedstock for cement clinker. An attempt to replicate this success in the UK is underway, but the difficulty is in obtaining the higher volumes required, in addition to a lot of testing that is required.
Recycled carbon fibre tailgate manufactured by Prodrive Composites in collaboration with ELG. © Inside Composites
Recycled carbon fibre tailgate manufactured by Prodrive Composites in collaboration with ELG. © Inside Composites
“It not economic for us to do it at the moment, but we have started working with waste contractor which is now collecting around 200,000 tons a year and we have started discussions with cement kilns to move this forward.”
Design
Gurit already places an emphasis on design in composites production to reduce reliance on petrochemicals, but Paul Spencer pointed out that composites have complex supply chains that are problematic, in addition to the high production energy use for carbon fibre production and the generation of a lot of waste in terms of fibres, as well as packaging and consumables.
“We also place an emphasis on lowering the toxicity of our products, as in our Bio Panel solution, which is based on a balsa-based structural core, natural fibres, lower-toxicity chemistry and bio-based resins,” he said.
Biocomposites were subsequently discussed and it was emphasised that they must be based on waste products not competing with food stocks or taking from other industries.
Martin Wright said he believed in the incremental progress now being achieved with drop in chemicals, even if currently achieving just 20-25% of bio-based content.
“Reaching those levels of bioderived materials still makes a big difference when you’re talking about, say 600,000 tons of PET resins, but we have to be careful that the bioplastics are exactly the same as what they’re replacing when it comes to recycling options, and not adding another layer of complexity. BioPET sits perfectly with existing process routes and products.
“It’s important not to greenwash and understand the perception of plastics as a whole by consumers. They don’t differentiate between PET bottles and carrier bags – it’s all plastic to them – but such incremental steps are part of the ladder we are climbing.”
ReDisCover
Lucy Eggleston argued that a radical transformation of both the raw materials and the processing routes involved in composites was called for, in addition to properly linking up the supply chain, which needs to be fully linked up and circular.
“At the National Composites Centre we are working with both academia and industry towards this,” she said. Our ReDisCover Composites programme, which next meets on November 12th has over 70 members and is undertaking a suite of projects based on four major themes – recycling, circular materials, disassembly and reuse.”