Maxim Segeren: Tree Composites is a Dutch startup founded in 2020 after 3 years of development at TU Delft in the Netherlands. The company has grown into a team of 25 experts with extensive experience in composite design and the manufacturing of composite joints for offshore wind foundations. We aim to accelerate the energy transition through the development of the novel composite wrapped joint technology, designed to revolutionise the manufacturing of jacket foundations. As the welding industry saying goes, “The best weld is no weld at all,” and that is exactly what we deliver. Our office and 800 m² workshop in Delft allow us to manufacture the composite joint using our in-house developed production method. Inspired by nature, our name comes from the way trees grow around steel tubes, placing fibres strategically to create an optimal connection. In 2017, inventor Marko Pavlovic saw a tree in his hometown of Belgrade, and that’s where the idea was born.
How the TC-joint replaces the traditional welding in TKY joints and what main assets it represents
for which sector(s)?
M.S.: Tree Composites’ joint technology leverages the strength and flexibility of composite materials to create joints that are more durable, lighter and produced with significantly less time and material than traditional welded joints in offshore structures. Compared to welding, loads are transferred over a wide area through a dedicated composite wrap rather than through the small surface of the weld. Our composite joint technology eliminates the value loss associated with welding steel for any joint type. The value gain of the composite joint is represented by a lifespan up to 5,000 times longer while reducing steel use by up to 50%. This breakthrough in connecting tubular members offers 3 additional benefits for offshore wind jacket foundations. By eliminating welding, we can double the production speed at construction yards, lower the cost per foundation and enable the reuse of foundations, which was previously not possible. Beyond steel, the technology can be applied to materials such as aluminium and can combine high-strength steel with mild steel without any penalties. These features make the technology widely applicable to virtually any lattice structure. As a result, TreeComposites enables offshore structures to be more cost-effective, sustainable, lighter and longer-lasting – even allowing for
reuse.
M.S.: Since the start of the company, we have been working closely with our clients and partners in the offshore supply chain to develop the composite joint in our R&D program. Direct partners in our program providing valuable in-kind and cash contributions are wind farm developers Vattenfall, Parkwind, and Shell; manufacturers and suppliers of steel structures HSM Offshore, Smulders and ArcelorMittal; and partners in design, testing and material supply TU Delft, Siemens Gamesa, Enersea, AOC and Buefa. We also receive support through national subsidies from RVO and NWO. Outside the consortium, we collaborate with Owens Corning and Chomarat for glass developments, and with Airborne and Pinette on automation development. These partnerships ensure an optimal product-market fit and provide the right partners to scale up to wind farm level…
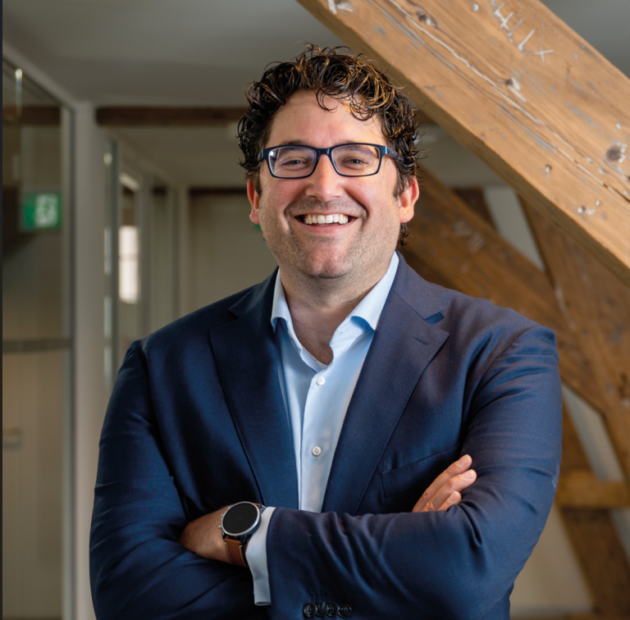
Photos: Tree Composites