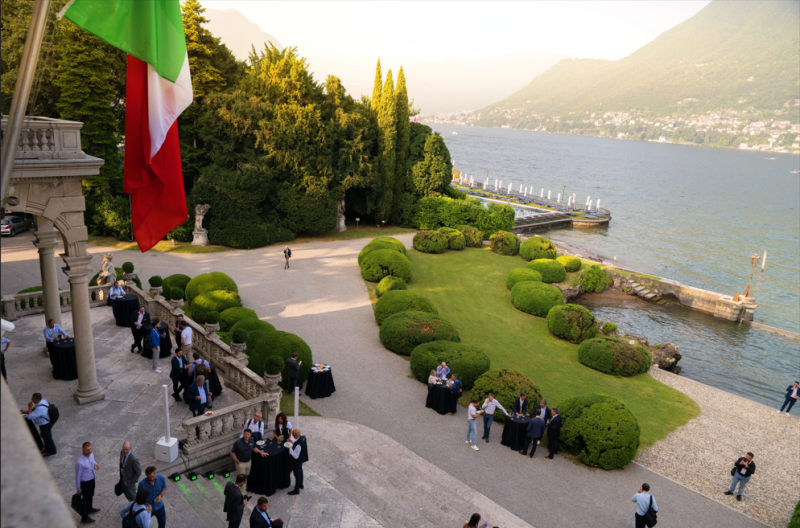
The 1,111 business meetings combined generated 1,916 leads for suppliers. As Roberto Frassine and Anne-Carole Barbarin underlined during the opening session: “There were more than 1,100 business meetings with the help of the event’s dedicated application, that made it easy to book appointments.” This year’s edition also celebrated the 20th anniversary of Assocompositi.
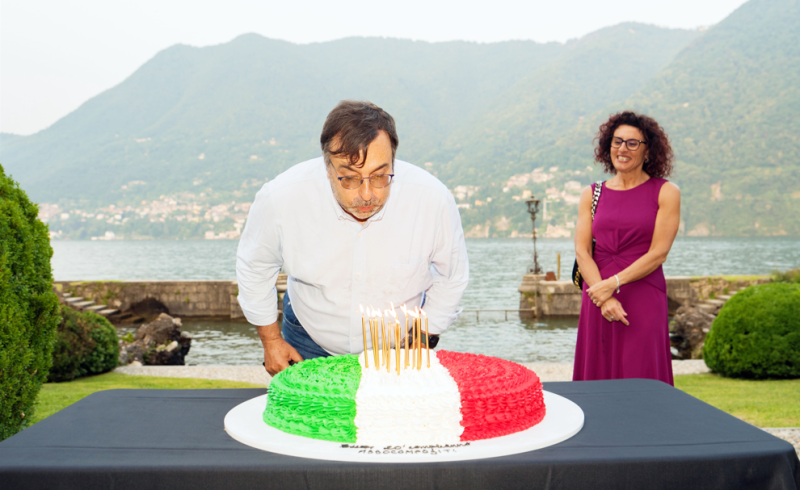
High-level technical insights
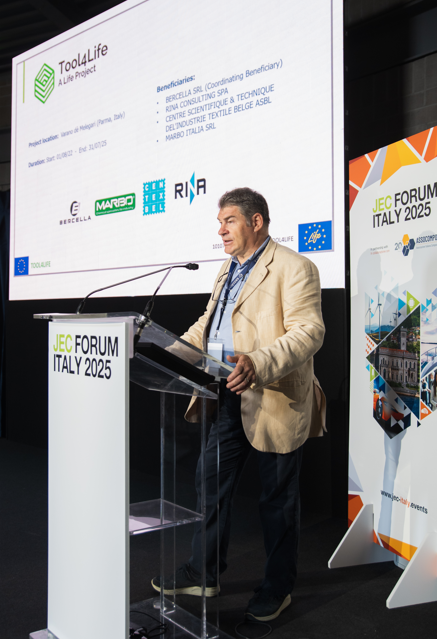
First day, among the standout presentations, Michele Morbarigazzi, Technical Project Manager at Bercella, detailed the European project Tool4Life, aiming to reinvent composite tooling with hybrid thermoplastic solutions and additive manufacturing. “It’s the core of our activity. We also have CNC finishing tools and a test lab,” he stated. Bercella’s focus on prepreg layup and autoclave curing — with 25 years of expertise — feeds directly into the Tool4Life concept: design-specific tooling that uses up to 25% polymer materials, cuts energy use by 33%, and reduces CO₂ by over 90% compared to standard approaches.
The project’s ambition is clear: tooling must withstand curing temperatures of up to 130°C for automotive parts and 180°C for aerospace components — a demanding challenge for thermoplastics. The integrated LSAM machine, capable of printing 50 kg/hour, was presented with a 3D-printed Maserati part on display, a tangible example of future-ready, more sustainable tooling.
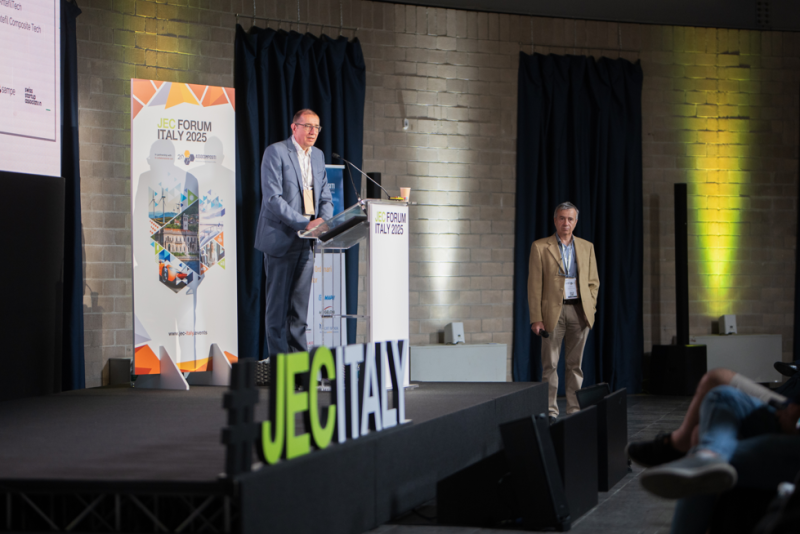
Professor Paoli Ermanni from ETH and co-founder of Antefil Composite Tech presented a promising alternative to thermosets: “Conversion is done simply through heat and a little pressure. Antefil develops & commercializes tailored composite materials based on hybrid glass fibers coated with various thermoplastic polymers. The coating takes place during the spinning process of the glass fiber. So the coating is inline with glass spinning. There is no compromise on speed or on efficiency”, says Paoli Ermanni. Antefil’s concept thus eliminates separate impregnation or curing stages.
Mobility, sustainability and performance
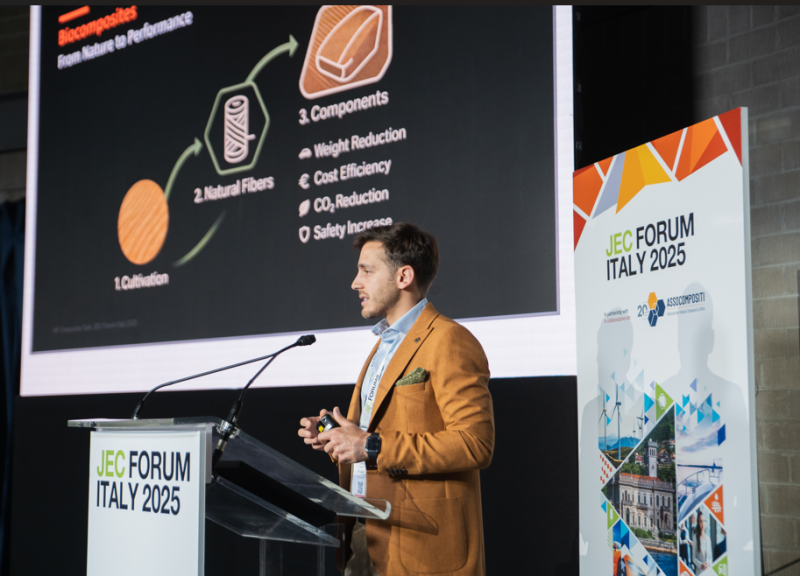
The Forum’s second day spotlighted transport applications. HP Composites, part of the Everspeed Group, shared its roadmap for motorsport and automotive structures under evolving safety and sustainability constraints. HP Composites’ studies on carbon-flax hybrids aim for lighter, safer, and greener structures, vital as motorsport faces stricter environmental rules. “We are exploring mechanical performances different from carbon. So we work on hybrid composites to combine the advantages of both materials,” explained Vincenzo Castorani.
“We are carrying out technical and numerical experiments, analysing each component separately and then hybridising them. At present, there is no standard test method for characterising the crashworthiness of composites. The machine used for the tests is an Instron. A number of crash tests have been carried out using different methods on different materials to test the different reactions, and this approach can be extended to other sectors such as aerospace, automotive and marine”, he explains.
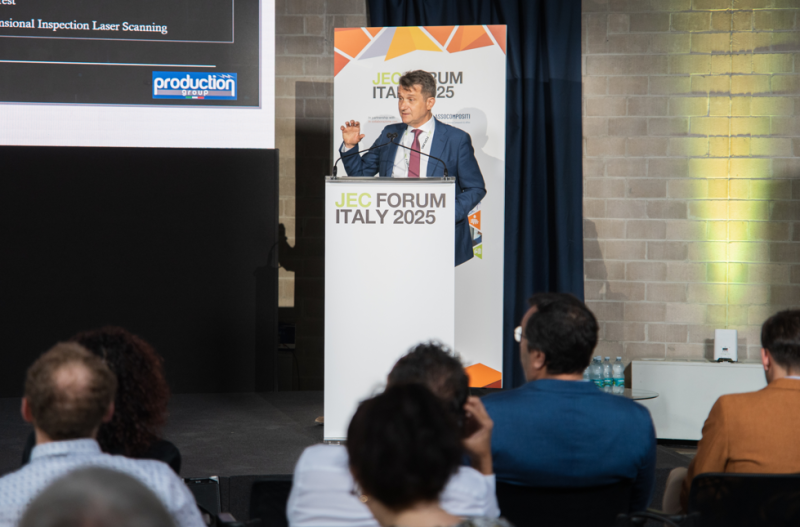
Rail transport also featured prominently. Dario Liguori from Production Group presented a breakthrough: re-engineering VHST (Very High-Speed Train) side skirts in composite instead of traditional aluminium. “The composite side skirt is 10% lighter, able to withstand static, fatigue, and aerodynamic loads prescribed by applicable technical specs & standard and in line with the budget, it’s lighter than the original design,” he said. The shift promises better corrosion resistance and easier maintenance, a significant step for rolling stock sustainability.
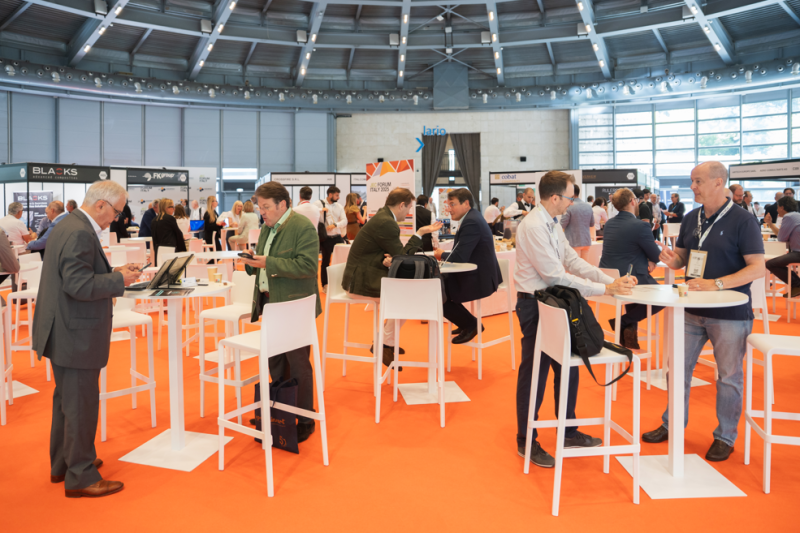
On the exhibition floor, leading companies like FK Group, Cobalt, Isomatex, Herambiente’s FIB3R, 3A Composites Core Materials and 64 others showcased the next generation of processing equipment, sustainable fibers, recycled carbon solutions, and award-winning core materials like the Thermhex and Diehl Eco luggage hold, winner of this year’s Crystal Cabin Award.