Bcomp’s technologies make it possible to replace parts traditionally made with carbon fibre for the past decades. One example: Exchanging carbon fibre composites for Bcomp’s high-performance natural fibre composites in the roof of the next-generation BMW M3 leads to a CO₂ reduction of around 40% in production plus additional end-of-life considerations.
Franciscus van Meel, CEO of BMW M GmbH, stated: “Natural fibre composites are a vital element of innovative lightweight solutions in motorsport, allowing for a reduction in CO₂e emissions in the manufacturing process. Natural fibre is an innovation that perfectly exemplifies BMW M’s claim ‘Born on the racetrack. Made for the streets.’. This is why we are delighted to confirm the series maturity of these materials, a breakthrough we achieved with our official BMW M Motorsport partner Bcomp. We are now looking forward to the use of these materials in future BMW M product ranges.”
From race-to-road: A collaborative journey
The roll-out of Bcomp’s materials into series production marks a race-to-road success. The long-standing and close partnership began with motorsport prototyping and has since delivered exceptional performance and sustainability gains across multiple racing platforms, including Formula E, DTM and GT4.
In 2019, Bcomp and BMW Motorsport pioneered the use of CO2 reduced materials in Formula E by using ampliTex™ and powerRibs™ materials to build a high-performance cooling shaft for the BMW iFE.20 race car. The 2022 BMW M4 GT4 brought the partners closer to the road, featuring more natural fibre parts than any GT race car to date — inside and out.
This transition from track to road has been further accelerated through strategic investment by BMW i Ventures into Bcomp’s funding rounds in 2022 (Series B) and 2024 (Series C). This financial and strategic support has played a pivotal role in scaling Bcomp’s solutions to meet the stringent requirements of exterior automotive components.
Marcus Behrendt, Managing Partner at BMW i Ventures, said: “At BMW i Ventures, we invest in young companies with the potential to bring innovations into large-scale production series. That is exactly what we identified in Bcomp leading the way for sustainable and innovative composites.”
Bcomp and BMW Group have developed a bespoke natural fibre colour and weave that even meets the stringent demands of roof structures in total vehicle homologation.
The public has already caught a glimpse of this unique material, which was used in the award-winning BMW M Visionary Materials Seat project.
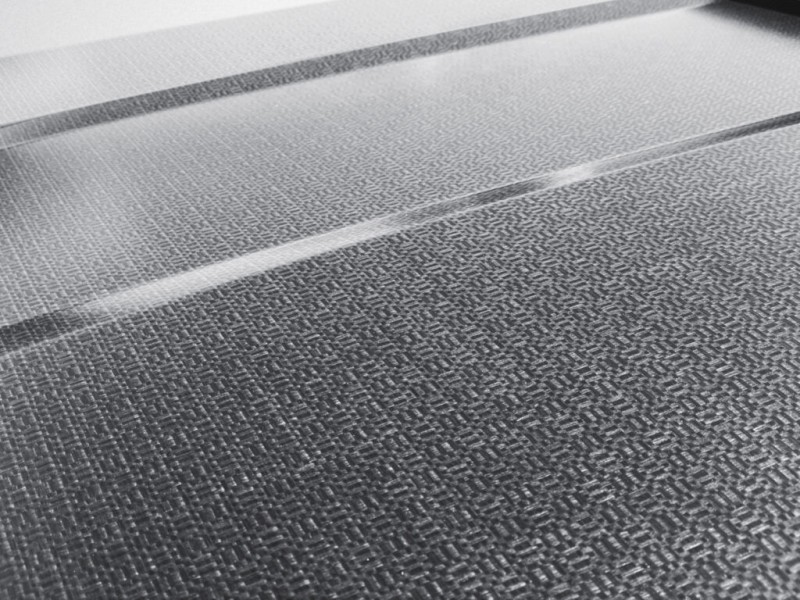
Race-track proven, industrial scale ready
The materials are designed to integrate seamlessly into multiple and existing manufacturing processes at scale. The roof will be made using a fully automated process called RTM (Resin Transfer Moulding), which makes production fast and consistent.
Other interior and exterior parts will be made using a prepreg process — a common industry method where fibres pre-impregnated with resin are shaped and cured in an autoclave (a high-pressure oven) to ensure high quality and stiffness. This underscores its commitment to vertical integration and enhanced control over performance, quality, and sustainability.
Johann Wacht, Manager Business Development & Strategic Customer Relationships at Bcomp, commented: “By collaborating with BMW Group we’ve been able to prove the performance of our innovative materials on the racetrack. Using these natural fibre-based materials on exterior parts of series road cars did seem impossible to many, but through our passionate teams collaborating closely we have been able to achieve the unthinkable. This work with BMW M acts as a lighthouse project that shows the automotive world what is possible when resilience, teamwork and big dreams join forces.”
Christian Fischer, CEO at Bcomp, adds: “Transforming a bold idea into a market-ready product demands not only technical excellence but also a shared commitment to challenge the status quo. Working closely with BMW Group, who have taken a solutions-orientated approach to this challenge, we’ve continuously strived to push the boundaries of innovation and worked as a team to overcome obstacles. The next step of this journey will see our materials used in series production cars, but our partnership won’t end there – after all, great innovators never stop.”