Denis Espinassou, Senior expert composite structure design & calculation, and Kouami Koutoati, Composite engineer, Cetim
In 2023, as part of its HyMEET strategic project, Cetim acquired a new HySPIDE TP® machine and is still working on the material, manufacturing and design of high-pressure R&D storage tanks development.
Simulations play a key role in this context and for this tank application. Model information can be used to increase the maturity of automated manufacturing processes, to improve the quality of composite fabrication, or to describe the material/structure response in a finite element model in order to design and justify product performance. Thus, 3 types of simulation are used.
Simulation of trajectories taking into account machine environment constraints
The composite laser welding process is carried out using a 7+2 axis robot and a head that, among other things, brings the tape into contact with a consolidation roller and welds it to the tank (Figure 1). The robot head is positioned as close as possible to the tank and the end of the boss. As a result, the winding angles are limited by the risk of collision and the shape of the boss.
A digital chain has been developed to simulate tape’s paths and robot’s kinematics in the whole environment (Figure 2). These simulations enable the product and process to be designed by acting on both the design of the boss and the design of the machine environment to minimise the gap between the composite and the boss. The digital chain set up has a very good level of fidelity but is still subject to variability in the liner geometry and tape slippage in its guiding elements which is validated by a final blank test.
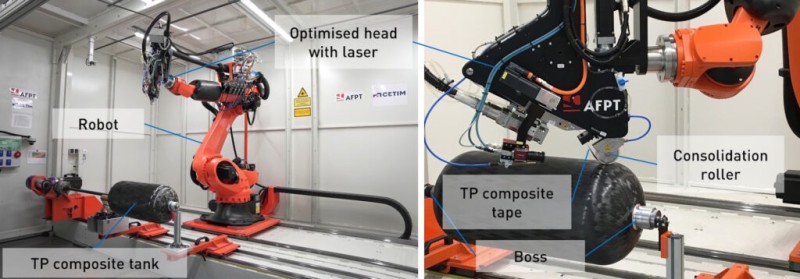
Simulation of the in-situ laser heated consolidation process
The LATP process is simulated using an optical-thermal-mechanical model. The main objective of the proposed model is to identify the best process parameters to ensure good consolidation during the bonding of the tape to the substrate. The simulation also focuses on the residual stresses by considering an anisotropic viscoelastic behaviour law and the thermal history of the part. The optical thermal model is based on several main hypotheses [1,2]. For the geometrical description, a 2D optical model has been considered (Figure 3). The absorbed heat from the laser irradiation is estimated using Fresnel and Snell-Descartes equations [3-4]. The multiple specular reflections of the laser light are described by a 2D ray tracing model [3-4]. The roller deformation was analytically described by the Hertz contact model [3].
The thermal model considered here is based on a 1D transient heat transfer model through the thickness z of the substrate and the deposited tape, with a Eulerian frame adopted to account for the material displacement [3]. The heat equation is completed by several boundary conditions and solved at each time step t with the finite difference method:
By considering the deposition rate as constant, each time step corresponds to a position along the substrate or tape length in curvilinear coordinate system s. The density ρ, the heat capacity Cp and the through-thickness thermal conductivity kz are considered as temperature dependent. The simulation of a deposition for a fixed process parameter (laser power, laser pivot angle, tape laying speed) can be performed, as well as a continuous tape deposition process using the laser power and laser pivot angle control script. The model was implemented in Matlab Code and was validated by experimental measurements using a thin thermocouple (Figure 4) and a thermal camera. Several outputs of the model are also computed for better analysis of the process parameters’ effects (laminated time above the melting temperature under the compaction, roller exit temperature, etc). The residual stresses are simulated in the commercial software Abaqus thanks to the developed mechanical model. The input is the thermal history obtained from the optical-thermal model. To better describe the temperature dependent behaviour of the composite, in particular the viscoelastic relaxation, a non-linear viscoelastic model [1] has been considered and implemented in a user subroutine. Current developments include the description of crystallisation effects in residual stresses arising during manufacturing.
Simulation of tank burst performance using Cetim’s Optitank tool
Type IV storage tanks are simple in appearance, but their material and structural behaviour are actually complex. In fact, each layer produced by the deposition of TP tape shows a change in thickness by tape superposition and a change in fibre orientation, particularly in the tank domes [5]. The anisotropy of composite materials requires perfect knowledge of the fibre distribution in order to predict the behaviour to design it to burst at a pressure above 1,575 bar. Cetim has developed an in-house tool, called Optitank (Figure 5), which can be used to predict thickness and angle evolution. The simulations carried out with this tool can be used to check the feasibility of manufacturing the winding (suitability of the trajectory, ability to consolidate the material, risk of cavity-type defects). This tool helps to avoid poor configurations and speeds up the fine-tuning phase of the manufacturing process.
A finite element model module is also included. The modelling choices are made to make the model more efficient in terms of computing time while maintaining assumptions that are faithful to the behaviour involved. An axisymmetric model was chosen to reflect the effect of thickness and curvature. The elementary behaviour of the layer is linear and anisotropic. A homogenisation strategy at the layer scale has been implemented to match the model assumptions as well as automatic post-processing to translate the stress components at the layer scale and in its material reference frame. The mesh and material orientations are automatically generated by the tool with an update for each deposition according to the previously deposited layer.
The strength of the Optitank tool lies in its ability to translate relatively complex concepts into simple but effective finite element modelling (linear static resolution with geometric non-linearities):
- advanced laws to describe thickness evolution within the layer, incorporating the specific features of thermoplastic composites;
- a multi-angle [±θi;…;±θn] definition model within each layer [5];
- a fibre resistance reduction law due to the winding pattern and out-of-plane deviations of the tape within a layer, contrasting with other approaches that aim to explicitly represent the tape and its winding pattern [6].
The global loop takes less than a minute without any special optimisation. This could make this model compatible with artificial intelligence learning processes.
Conclusion
This whole modelling strategy is currently used in various development projects at Cetim, in line with the objectives of burst > 1,575 bar as already demonstrated by Cetim [7], but also for other typical load cases of tank validation.
As part of its technology transfer mission, Cetim is committed to disseminating these methodologies to make them accessible. To this end, Cetim is working with S-vertical to integrate the philosophy of its Optitank tool into the WoundSim software.
References
[1] Di Gennaro Livio, “Modeling and simulation of the initial state of a thermoplastic matrix composite structure manufactured by laser assisted tape placement”, 2022 (Thèse de doctorat), Université Paris-Saclay
[2] Le Louët Violaine, “Etude du comportement thermique de bandes composites pré-imprégnées au cours du procédé de fabrication AFP avec chauffage laser”, 2018 (Thèse de doctorat), Université de Nantes
[3] Kok Thijs, “On the consolidation quality in laser assisted fiber placement: the role of the heating phase”, 2018, University of Twente
[4] Grouve Wouter, “Weld strength of laser-assisted tape-placed thermoplastic composites”, 2012, University of Twente
[5] Damien Guillon, Denis Espinassou, Pierre Pichon, Juan Javier Rojas Carrillo, Charlotte Landry, David Clainchard, Laurent Juras, Romain Brault, “Manufacturing, burst test and modeling of high pressure thermoplastic composite overwrap pressure vessel”, Composite Structures Volume 316, 15 July 2023, 116965
[6] Gaspard Landron, Alain Rassineux, Christophe Bovet, Christian Fagiano, Martin Hirsekorn, Emmanuel Baranger, Denis Espinassou, “Geometric validation of a tape-scale mesh generation tool of a filament-wound hydrogen tank”, Proceedings of the 21st European Conference on Composite Materials (ECCM21), 2-5 July 2024, Nantes, France
[7] https://www.svertical.com/post/thermoplastic-composite-for-serial-production-a-concept-becoming-possible