Chris Skinner: Two years ago, I was part of the JEC Startup Booster 2024, with Owens Corning as a sponsor. Guillaume Perben made a very clear presentation and the jury selected him. He proposed a good model and approach to recycling, using thermolysis to convert waste composites into secondary raw materials. That’s when we started working together.
So you’ve been working together since 2024. How far have you come?
We worked together on assessments of what his process could produce. Our process, Sustaina Loop, which combines post-industrial circular glass fibres with traditional glass-based materials, makes it possible to use post-consumer recycled fibres and reintegrate them into new products, while Composite Recycling’s process is designed to remove the resin from the fibres. So it came at just the right time.
How should this collaboration develop in practical terms?
As part of the collaboration, the two companies will conduct technical trials to assess the commercial feasibility of incorporating recycled materials into Owens Corning’s glass reinforcement production systems. Together, the two companies will work towards the industrial scale-up of Composite Recycling’s technology to make the process cost-effective and efficient on a large scale, addressing the challenges of recycling composite waste across multiple industries.
We will jointly develop and refine methodologies for incorporating recycled materials into Owens Corning’s glass fibre production streams for use in industries such as boating, automotive, transportation, aerospace and building materials.
The relationship will also cover compliance with industry regulations and standards. Our two companies have signed a letter of intent to agree the content of the partnership and the next steps. They expect to finalise a formal agreement within the next 12 months, which will pave the way for exploring further opportunities for the use of recycled composite materials in Owens Corning’s diverse range of glass reinforcement products.
What are the technical stages of this collaboration?
First of all, we characterise the fibres before reusing them. The majority of Composites Recycling’s fibre comes from the marine sector. We work with other partners in the wind energy sector. We then put the fibre back into the furnaces and transform it into a normal, continuous glass fibre that can then be incorporated into our range of sustainable fibres to produce automotive parts, building materials and insulation products. For our Sustaina Loop range, we can use 10% recycled content, charged by mass balance.
The shift toward recycled content is no longer a trend, it’s a necessity. As consumer and regulatory pressure increases, this collaboration enables us to provide our customers with the solutions they need to meet these challenges and the growing demand for sustainable solutions. Our collaboration is now mature enough to enable these fibres to be integrated into boats.
Groupe Beneteau, Veolia, Owens Corning, Chomarat, Arkema and Suez formed an alliance earlier this year with Composite Recycling, which aims to create a circular model of boat construction and design using recycled materials.
Beneteau will use recyclable composite materials, in particular Arkema’s Elium resin, to manufacture its boats. Veolia will recover composite production off-cuts and transport them to its recycling site in western France, where Composite Recycling has set up its thermolysis technology to separate and recycle glass fibre-reinforced composites. Arkema will transform the oil from thermolysis into new Elium resin, while Owens Corning will produce new glass fibres from the recovered fibres and Chomarat new glass fibre reinforcements. To complete the picture, Groupe Beneteau will reuse Elium resin and recycled glass fibres to manufacture new boats.
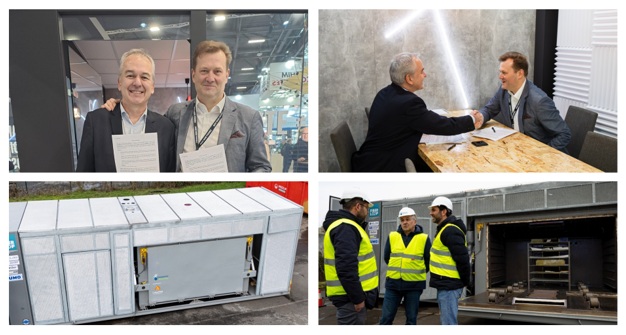
Top Row: Guillaume Perben (left) and Chris Skinner (right) sign the agreement at JEC World 2025 in Paris.
Second Row: Composite Recycling’s first industrial-scale recycling unit near Nantes, France will keep 400 tons of composite waste out of landfills annually.