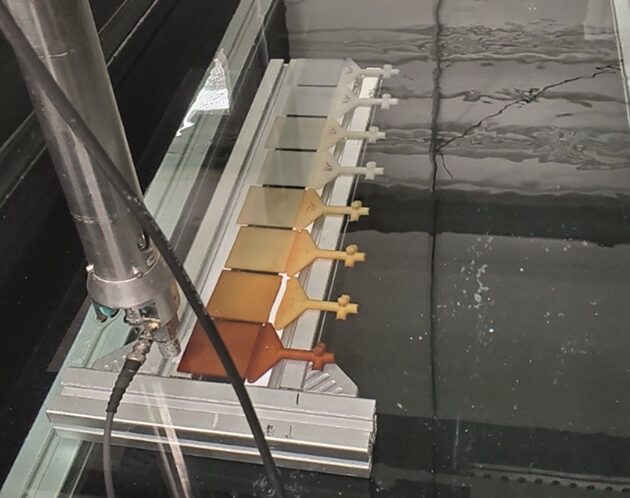
Fig. 1: Ultrasound measurement device
For semi-crystalline polymers, the crystallinity rate is a key parameter which directly influences mechanical properties, such as mechanical resistance or stiffness, as well as thermal and gas barrier properties. The crystallinity rate is usually determined using a differential calorimetry technique (DSC), but this is a destructive method for the final product and, moreover, it cannot be applied for in-situ or continuous control. The development of a non-destructive and in-situ methodology for the estimation of the local crystallinity rate is therefore a major advance for quality control, as it provides a complete cartography of properties over the entire part without the need to take samples of the part for destructive testing.
Using ultrasounds to determine elastic properties
Ultrasonic measurements can be used as a powerful tool for determining the elastic properties of materials. It has been shown that both ultrasound speed and density are directly related to mechanical stiffness. The measurement of these velocities along the main directions can lead to the direct determination of some of the terms of the elasticity tensor of the material. The measurements can be orientated to take account of the anisotropy of the material. based on this observation, Canoe has set up a methodology that highlights an accurate determination of the ultrasound speed velocity in the material in order to directly determine a relationship to crystallinity rate.
The methodology
A methodology has been developed to study this correlation. A polyamide 11 (PA11) semi-crystalline polymer has been selected, and 8 specimens were manufactured using an identical process (injection moulding). The specimens were placed progressively in a high-temperature oven (150°C), above the glass transition temperature but below the melting temperature, for between 1 h and 1 week, with 6 intermediate times, in order to gradually increase the crystallinity rate by curing. The cooling was naturally made at room temperature. Afterwards, the speed of ultrasounds was measured on the whole surface of the specimens. An immersion measurement technique was used to ensure consistent acoustic coupling properties. All the samples were placed into a waterfilled tank (water absorption to PA11 was ignored) for inspection (Figure 1). They were monitored using a focused 0.5 in diameter and 5 MHz single element transducer. The thickness of each sample was preliminarily measured with a calliper (accuracy 0.01 mm). The time of flight of the ultrasound waves through the sample could be measured and was used to calculate the ultrasounds velocity (accuracy about 16 m/s). A full measurement cartography was drawn up over the entire surface of the specimens with a 1 mm step along the 2 main axis (Figure 2).
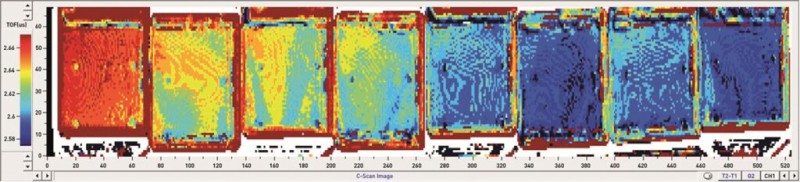
Fig. 2: Time of flight of ultrasound waves through the specimens
After the ultrasound inspection, a sample was taken for each specimen. For each sample, the crystallinity rate was measured using the DSC technique during the first heating under N2 at 10°C/min. These results were compared to the ultrasound measurements to establish a law between the 2 techniques.
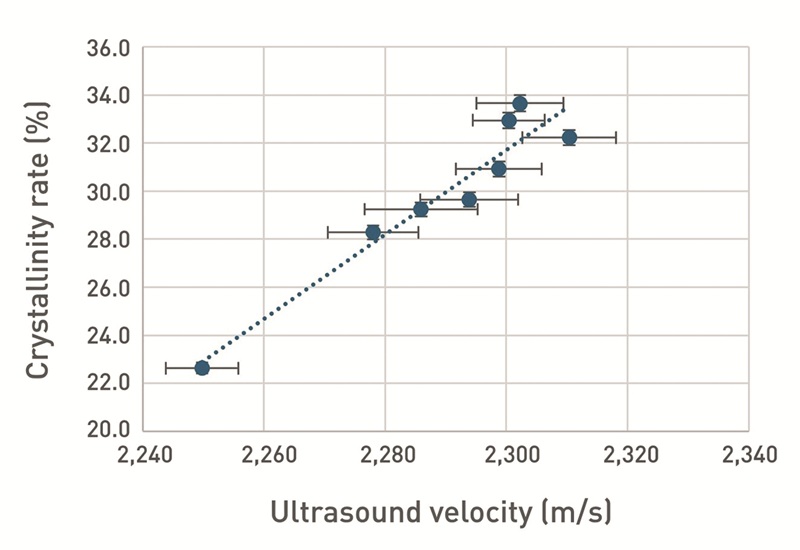
Experimental results
Figure 3 shows a plot of the crystallinity rate versus the averaged ultrasound velocity measured on each specimen in the area where the sample for DSC was taken. For each sample, the standard deviation of the speed measured over the whole specimen is also presented. It is clearly visible that there is almost a linear connection between the crystallinity rate and the ultrasound velocity (R²=0.92), despite a significant standard deviation, most likely reflecting a gradient of crystallinity over the whole surface of each specimen. The calculated correlation coefficient between these 2 properties is about 95%. It is worth noticing that the mechanical stiffness also depends on density, which is also affected by the crystallinity rate. The geometrical density was also measured for each specimen and used to calculate the corresponding coefficient of the elastic tensor (noted C33, in MPa). The results (Figure 4) show excellent linearity in the behaviour between these 2 parameters. The R² is maintained at around 0.93.
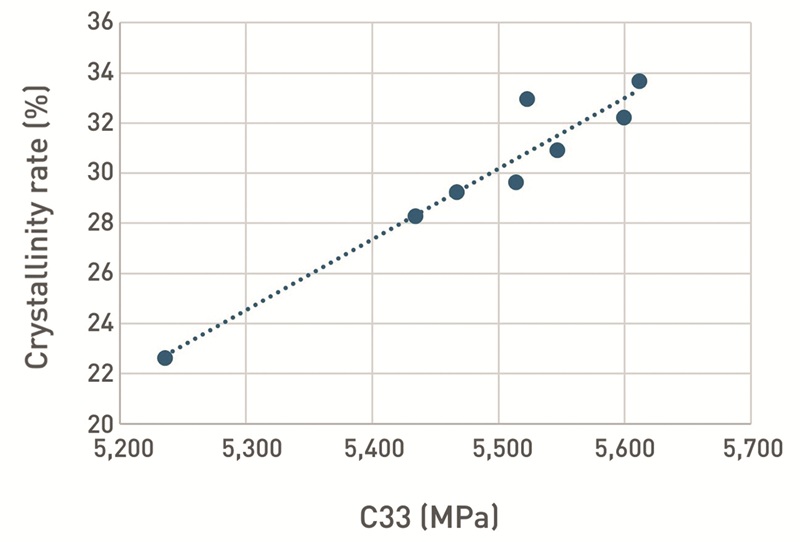
An easy and effective measuring tool
The results presented in this study highlighted the fact that it is possible to estimate the crystallinity rate using a simple measurement of the ultrasound velocity. This correlation was made possible by the strong relationship that exists between stiffness and ultrasound velocity in all materials.
In this case, the immersion technique was used for ultrasound measurements, as it is an easy and convenient way of automatically monitoring an entire surface. But the ultrasound velocity can also be determined using many other ways, for example using portable devices that allow in-situ measurements to be taken directly on a structure. The measurement is fast, reproducible and accurate. It can be applied to a wide range of materials and structures, as long as the geometry and attenuation properties of the ultrasound wave propagation allow correct measurement. However, knowledge of the material’s behaviour, and more specifically of the quantitative relationship between ultrasound speed and crystallinity rate, is required to make a quantitative measurement. This relationship can be determined using standard blocks during a preliminary study. The methodology can highlight property gradients at the surface of the inspected part and can be used for quality control of a final manufactured part.
The efficiency of the methodology still needs to be demonstrated on composite materials, where the presence of fibres or loads and the induced heterogeneity of the material structure can have a significant impact on the speed of the US waves, in addition to the crystallinity rate.