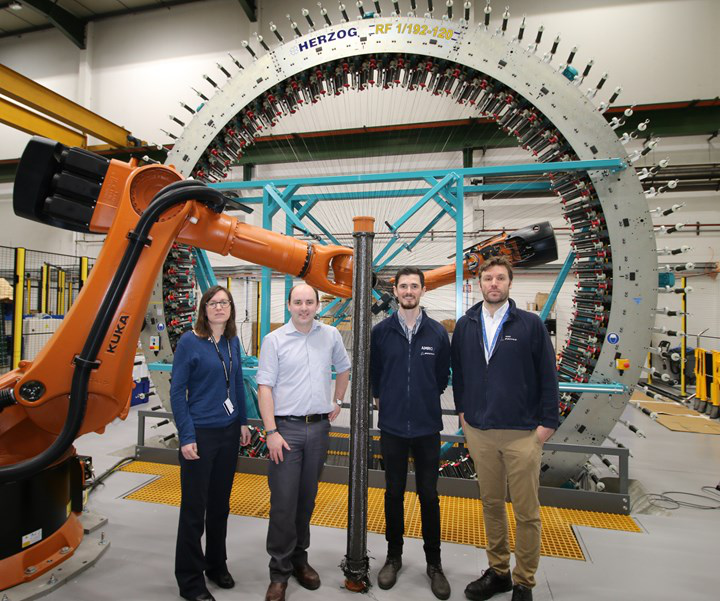
The AMRC Composite Centre team that is developing the technologies as part of the ?20 million project. Source | AMRC
Composite researchers at the?University of Sheffield Advanced Manufacturing Research Centre <https://www.amrc.co.uk/> (AMRC, Sheffield, U.K.), along with industry partners from the High Value Manufacturing Catapult <https://hvm.catapult.org.uk/>, are carrying out a 20 million (more than $25 million USD) project to develop lightweight composite?propeller blades aimed at reducing the U.K. aviation sector’s?carbon footprint and noise emissions at airports.?
The AMRC, along with the National Composites Centre (Bristol, U.K.) and the Manufacturing Technology Centre (Coventry, U.K.), is supporting private sector partner Dowty Propellers (part of GE Aviation Systems) for the Innovate UK-funded Digital Propulsion project.
Alongside the NCC, the AMRC?is exploring innovative ways to design and manufacture various types and sizes of propeller blades, including?the load bearing structure, the cores, the blade roots and relevant hub connections. The researchers are also collaborating to form a new braid that fits various shapes, using equipment purchased by the AMRC with funding from the Aerospace Technology Institute (ATI).
“Our portfolio of cutting-edge equipment means we’re able to access a wide range of advanced technologies to do this work including finite element analysis, braiding, tailored fiber placement, resin transfer molding and press forming,” says Elaine Arnold, automation technical lead for the AMRC Composite Centre.
“The next steps will be to look at the braiding of multiple parts of the blade and then the thermoforming of the foam that sits on the inside of the blade. Excellent progress has been made so far and the goal is for us to make a section of the full blade,” Arnold adds.
The three-year program has allowed Dowty to investigate multiple technologies to design the next generation of composite propeller blades, incorporating new and novel geometries beyond current capabilities offered by existing manufacturing techniques.
“This program?paves the way for new business opportunities within Dowty. The technology development led by the Catapults is allowing us to explore both current and emerging markets and create offerings for prospective customers which are both innovative and cost effective. The cross-Catapult collaborative effort is enabling detailed technology development to occur at a fast pace due to the sharing of resource and expertise, all of which benefits Dowty and, ultimately, its customers,” says?Jonathan Chestney, Dowty Propellers’ engineering leader.
The AMRC is working with Catapult colleagues in the Bristol based National Composites Centre and the Coventry based Manufacturing Technology Centre in the ATI-funded program. They are also investigating the shift from manual to automated blade manufacturing processes.